AGXWire¶
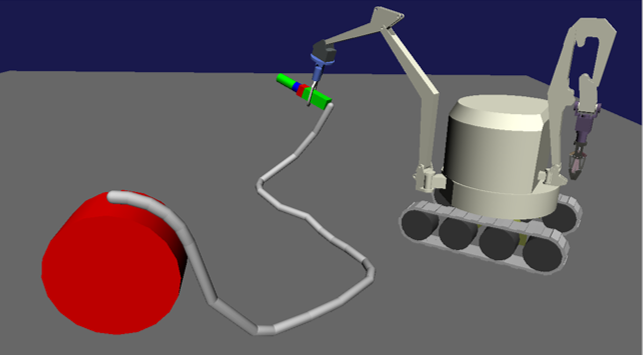
AGXWire is a wire model using AGX Dynamics. The agxWire module of AGX Dynamics is used for implementation.
Features of AGXWire¶
Hard to be torn
Even if the wire is pulled with a strong force it is hard to be torn. For example, it is useful for hanging a container with a crane wire.
Good performance for long length
A general physics engine expresses cables and wires by connecting rigid bodies with a shape such as a capsule and a cylinder with joints.Therefore, as the number of rigid bodies increases, the amount of computation increases, and finally the calculation is not completed within real time.In this model, the number of elements can be automatically increased / decreased during the simulation.This can be reduce computation amount of the simulation.
Note
Sample¶
You can check samples to how to use AGXWire. The samples are below. When loading the sample projects with Choreonoid and running the simulation with AGXSimulator, the wire will be displayed.
- Winch, Wire, Wire link
- Project file: chorenoid/sample/AGXDynamics/agxWireSample.cnoid
- Body file: chorenoid/sample/AGXDynamics/agxWireSample.body
- Fire hose
- Project file: chorenoid/sample/AGXDynamics/FireHose.cnoid
- Body file: chorenoid/sample/AGXDynamics/FireHose.body
How to write¶
Link composition of sample model is as below.
links:
-
name: Drum
parent: Root
translation: [ -1.0, 0.0, -3.0 ]
jointType: fixed
elements:
-
type: Shape
geometry: { type: Cylinder, radius: 0.25, height: 0.2 }
appearance: { material: { diffuseColor: [ 1.0, 0, 0 ] }}
-
type: AGXWireDevice
radius: 0.02
resolutionPerUnitLength: 5
collision: true
selfCollision: true
materialName: Wire
#wireYoungsModulusStretch: 6E10
#wireSpookDampingStretch: 0.075
#wireYoungsModulusBend: 6E10
#wireSpookDampingBend: 0.075
Winch:
linkName: Drum
position: [ 0.0, 0.0, 0.27 ]
normal: [1.0 , 0.0, 0.0 ]
pulledInLength: 50
haulForceRange: [ -50, 50 ]
Nodes:
-
type: free
linkName: Root
position: [ -0.27, 0.0, 0.27]
-
type: free
linkName: Root
position: [ 0.27, 0.0, 0.27]
-
type: link
linkName: Sphere
position: [ 0.0, 0.0, 0.1]
#twistStiffness: 1.0E10
#bendStiffness: 1.0E10
#superBendReplacedWithBend: true
-
name: Sphere
parent: Root
translation: [ 1.0, 0.0, 0.0 ]
jointType: free
mass: 1.0
elements:
-
type: Shape
geometry: { type: Sphere, radius: 0.1 }
appearance: { material: { diffuseColor: [ 0.0, 1.0, 0 ] }}
-
type: AGXWireDevice
radius: 0.04
resolutionPerUnitLength: 5
collision: true
selfCollision: true
materialName: Wire
Nodes:
-
type: link
linkName: Sphere
position: [ 0.0, 0.0, -0.1]
-
type: fixed
linkName: Box
position: [ 0.0, 0.0, 0.1 ]
-
name: Box
parent: Sphere
translation: [ 0.0, 0.0, -2.0 ]
jointType: free
mass: 5
elements:
-
type: Shape
geometry: { type: Box, size: [ 0.2, 0.2, 0.2] }
appearance: { material: { diffuseColor: [ 0.0, 1.0, 0 ] }}
- Add AGXWireDevice to the elements part of arbitrary link
- Set parameters of the wire
- Set the radius of the wire to the parameter radius
- Set the resolution of the wire to the parameter resolutionPerUnitLength
- Set enable or disable collision between wires, links and other environments to collsion
- Set enable or disable self collision between the wire and the links which has the wire to selfCollision
- Set the material of the wire to materialName. Check the reference Additional parameters for physical material.
- It is recommend to use the material file. Though, you can set parameters such as wireYoungsModulusStretch directly into the body file.
- In order to pull out the wire from the winch, set the following
- Set the link name, which to be used as a winch, to linkName. You can specify any link.
- Set the pulled out position of the wire to position relative from the link coordinate of the link
- Set the pulled out direction of the wire to normal relative from the link coordinate of the link
- Set the length of the wire which stock into the winch to pulledInLength
- Set the required force to pull out the wire from the winch or put in to haulForceRange
- Next, use the Node hash to route the wire in space
- Wires can be routed in three ways. The way of routing is specified as type:
- type: free Route the wire to the specified position. Not fixed.
- type: fixed Fix the wire at the specified position. The fixed point can rotate freely(balljoint).
- type: link Connect the wire to the link. The connecting point has twisting stiffness and bending stiffness.
- Set the linkName in which coordinate system to route the wire
- When the link exist in which name is the linkName: Link coordinate
- When the linkName is empty or not exist link: World coordinate
- Set the routing position to position
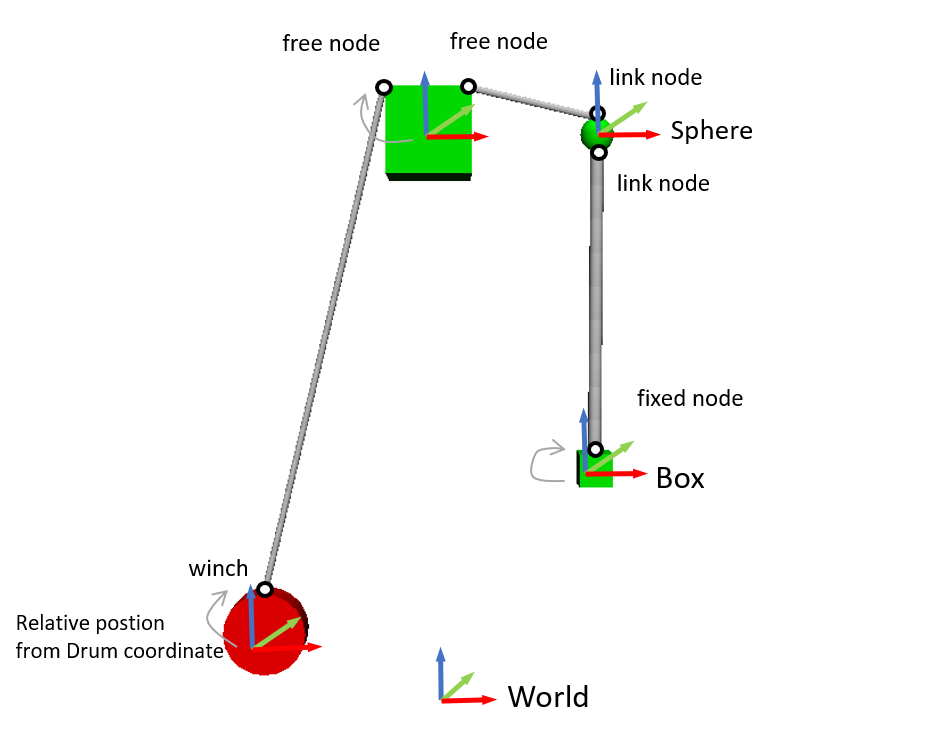
Explanation of parameters¶
The parameters are described below.
Wire
parameter | default value | uinit | data type | explanation |
---|---|---|---|---|
type: AGXWireDevice | - | - | string | declaration of using AGXWire |
radius | 0.02 | m | double | radius of the wire |
resolutionPerUnitLength | - | m | double | minimum resolution of the wire |
collision | - | - | bool | set enable/disable collision between the wire and other objects |
selfCollision | - | - | bool | set enable/disalbe self-collision between the wire and the body which has the wire |
materialName | - | - | string | name of the material |
wireYoungsModulusStretch | 6e10 | N/m | double | young’s modulus in the stretch direction |
wireSpookDampingStretch | 0.075 | s | double | spook damping in the stretch direction |
wireYoungsModulusBend | 6e10 | N/m | double | young’s modulus in the bending direction |
wireSpookDampingBend | 0.075 | s | double | spook damping in the bending direction |
twistStiffness | 0 | N/m | double | Available at type:link. Twisting stiffness between the wire and the link. |
bendStiffness | 0 | N/m | double | Available at type:link. Bending stiffness between the wire and the link. |
superBendReplacedWithBend | false | - | bool | Available at type:link. Make the wire more flexible in the bending direction at the connecting point. |
Winch
parameter | default value | uinit | data type | explanation |
---|---|---|---|---|
linkName | - | - | string | link name which to be a winch |
position | - | Vec3 | pulled out position of the wire | |
normal | - | Vec3 | pulled out direction of the wire | |
pulledInLength | m | double | length of the wire which store into the winch | |
haulForceRange | N | Vec2 | force required to pull out the wire from or put in the wire to the winch |
Node
parameter | default value | uinit | data type | explanation |
---|---|---|---|---|
type | - | - | string | type of routing the wire: set free, fixed, link |
linkName | - | - | string | link name in which coordinate system to route the wire |
position | - | Vec3 | position where locate or fix the wire |
Collision settings of the wire¶
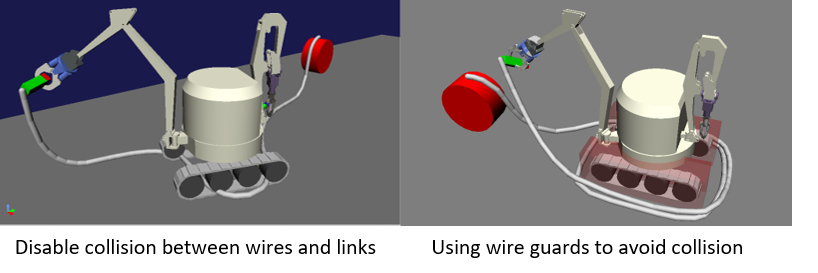
Disable collision with the specified link with the wire¶
As shown in the above left figure, disable collision between the wire and the specified link. This can be done by setting excludeLinksWireCollision of the collision setting of Additional parameters for body model.
collisionDetection:
excludeLinksWireCollision: [ linkQ, linkR, ... ]
Attach a wire guard to the link to avoid collision with the wire¶
Another way is to attach a guard to the link which you want to avoid collision with the wire as shown in the above right figure. This can be realized by describing it in the body file as follows. Add a guard link to the body file. However, since it will cause collision with other links and self collision as it is, set excludeLinksDynamic and disable collision between links. Then the guard link will collide with the wire only.
-
name: WIRE_GUARD_L
parent: TFRAME
jointType: fixed
translation: [ -0.02, -0.595, 0.600 ]
material: default
elements: &WireGuard
-
type: Collision
elements:
-
type: Shape
geometry: { type: Box, size: [ 2.1, 1.5, 0.5 ] }
collisionDetection:
excludeLinksDynamic: [ WIRE_GUARD_L, WIRE_GUARD_R ]
Specification¶
- Please note that wire material parameters are overridden in the order of material description < direct description .